The Unboxing
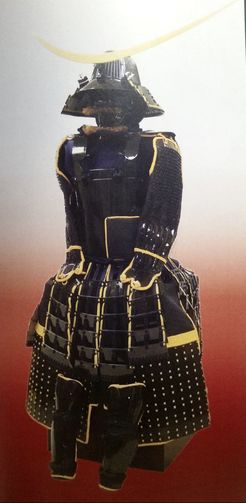
I haven't had the chance to build a scale model kit in years primarily because of work. I've always put off “just for fun” projects. Not to say that some of my work projects haven't been fun to work on. But this one combines the best of both worlds.
My build diary in the ModelSpace Forum will focus on the mechanics of putting the armor together. I'll also have a supplemental posts here, on my blog at russogi.com/blog with insights and other thoughts I have about the armor design and construction and how it has, or will influence my art.
For a more detailed introduction about who I am and my reason for undertaking this project you can go to my introductory post here in the ModelSpace Forum or here on my personal blog.
Now on to the unboxing.
I ordered the entire kit rather than a part-work subscription. So if you're wondering what it looks like when the entire kit arrives in one shot, here it is.
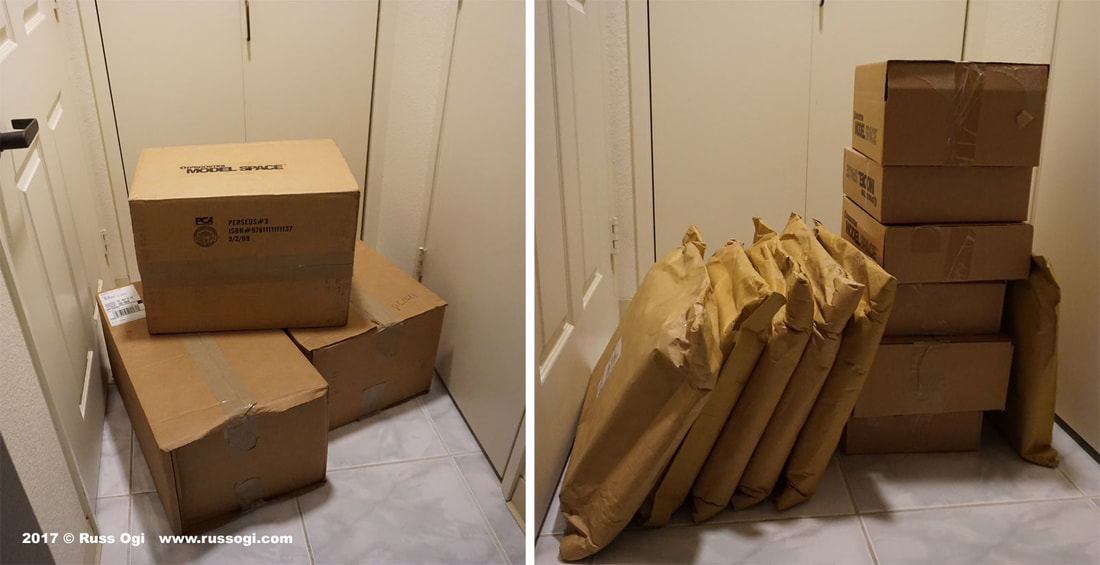
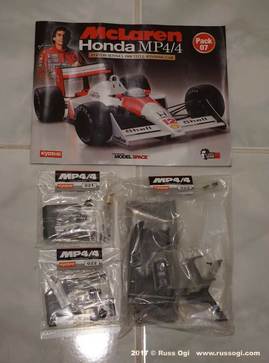
In case you missed it in the gallery above, one of these things is not like the others.
Kidding aside, somehow this Pack 7 for the MP4/4 was mistakenly included in my kit in place of the Samurai armor Pack 7.
In addition to the incorrect Pack 7, the Yoroi bitsu (armor storage box) is missing. The yoroi bitsu serves as both storage container for the armor and as the base for the wooden display stand to sit.
I quickly contacted DeAgostini customer service and informed them of the errors.
The correct Pack 7 was dispatched at no charge to me. It did take about 2-3 weeks to make it to me but, being in Hawaii, you accept longer shipping times as part of the price of living in paradise.
Trying to get the storage box however is an on going issue. More on that later.
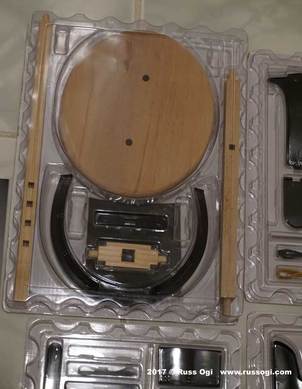
The model itself is made of multiple materials including metal, wood, faux leather and multiple types of material. The kote (armored sleeves) are made of chain-mail. Half scale chain-mail, how cool is that!
I've been reviewing the instructions online and reading the build diaries of others on the ModelSpace Forum to get an idea of what's ahead.
Since I have the entire kit, I am planning on building the armor in sections rather than following the steps in order. For example, lacing all the kusazuri (tassets) sections at the same time. I find when I work, it's much easier, and more enjoyable, to tackle similar tasks together.
But building out of order presented the problem of keeping parts from getting lost and keeping them organized. There are a lot of parts and many of them are much smaller than they look in the instructions.
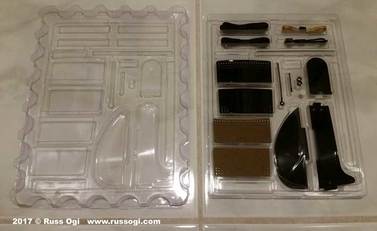
Both top and bottom are contoured to keep the parts in place and snapped together at several points keeping top and bottom securely closed.
This allows me to use them as storage containers making the parts accessible while keeping them organized.
I'll be following up shortly with another post as I start the build. If you have ever worked on a project like this or have any model making tips, please share your thoughts or stories in the comments below.